Carrying out nucleic acid testing can quickly detect virus infected persons, which is a very important strategic measure for COVID-19 prevention and control. At the same time, the safety of nucleic acid testing sites should not be neglected, and we should strengthen control and disinfection to prevent the risk of infection.

Staffing and Protection
Each sampling site should be equipped with 1-2 sampling personnel. Reasonable arrangement of sampling personnel rotation, in principle, every 2-4 hours to take a rest.
Requirements for protective equipment for sampling personnel:
1. work clothes
2. Protective Clothing/Isolation Gown
3. Shoe Covers/Gum Boots
4. N95 masks
5. Disposable sanitary cap
6. Goggles/visor
7. Disposable latex gloves, etc.
Preparation of disinfection supplies
1. 75% alcohol
2. Chlorine Disinfectant
3. Watering can
4. Constant sprayer
5. Ultra Low Volume Nebulizer/Air Sanitizer (Indoor)
6. Cleaning cloth
7. Mop with bucket
8. Antibacterial hand sanitizer
9. Dry toilet paper
10. Hand sanitizer
11. Trash can (large/medium)
12. Medical garbage bags (large/medium/small)
13. Medical waste labels, etc.
Disinfection requirements for nucleic acid sampling points
The environment of the sampling point, including surfaces and air, should be disinfected at any time.
1. Hand hygiene
Medical staff engaged in sampling should do personal protection and implement hand hygiene in accordance with standard norms. Wear double-layer latex gloves if they come into contact with the patient’s blood, body fluids, secretions or excrement; if the gloves are contaminated, replace the outer latex gloves in time. Strict hand disinfection or changing gloves should be carried out for each person collected.
2. Object surface
Tabletops, seats and other surfaces should be disinfected at any time. Use chlorine-containing disinfectant with an effective chlorine content of 1000mg/L or 75% alcohol to wipe and disinfect, and the action time should not be less than 30 minutes.
3. Office facilities
Computer keyboards and mice, electronic equipment and non-corrosion-resistant items can be cleaned and disinfected with 75% alcohol at any time.
Note: When disinfecting with 75% alcohol, the electronic equipment should be powered off; avoid close to the heat source; do not use alcohol for large-scale spray disinfection!
4. Indoor air disinfection
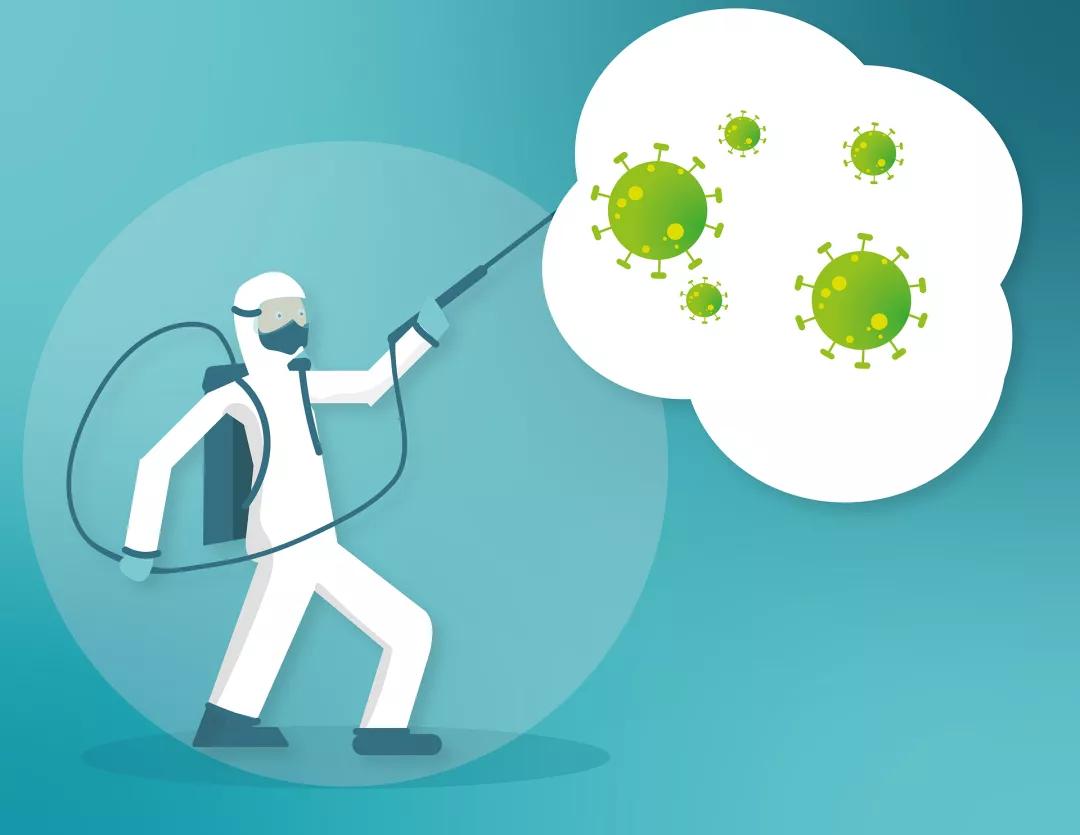
5. Preventive disinfection
Open windows for ventilation at least 2-3 times a day, each time not less than 30 minutes. If physical methods cannot be used, chemical methods can be used.
It is not advisable to open windows for ventilation, and mechanical ventilation equipment or air disinfection equipment that meets the requirements should be installed for air disinfection.
Ultraviolet rays can also be used to sterilize the air under unmanned conditions. When using ultraviolet rays to sterilize, the irradiation time can be appropriately extended to more than 1 h.
6. Terminal disinfection
In the case of no one indoors, use disinfectants such as 30 000 mg/L hydrogen peroxide, 5 000 mg/L peracetic acid, 500 mg/L chlorine dioxide, etc., and use an ultra-low volume sprayer. Use 30 mL/m3 for spray disinfection.
Action time: 30-60 min for hydrogen peroxide and chlorine dioxide, and 1 h for peracetic acid.
After disinfection, open doors and windows for thorough ventilation.
Disinfection of sampling staff
After the disinfection work is completed, the personnel and equipment need to be disinfected. Two staff members alternately disinfect personnel, from the head and face to the soles of the feet (front and back sides) in turn. Special attention should be paid to the easily neglected parts such as armpits, soles, and crotch. For the disinfection of the instruments, two staff members alternately perform full-coverage disinfection of the sterilized instruments. Finally, sanitize your hands.
The non-reusable protective equipment is used as medical waste, and it is packaged after disinfection treatment, and the packaged outer packaging is sprayed and disinfected and transported; the reused protective equipment is then soaked or sprayed for disinfection.
Note: It is not recommended to directly use disinfectants to disinfect personnel for scientific and precise disinfection. In special cases, personnel must be disinfected under the condition of intact secondary protection to avoid damage to the human body caused by disinfectants.
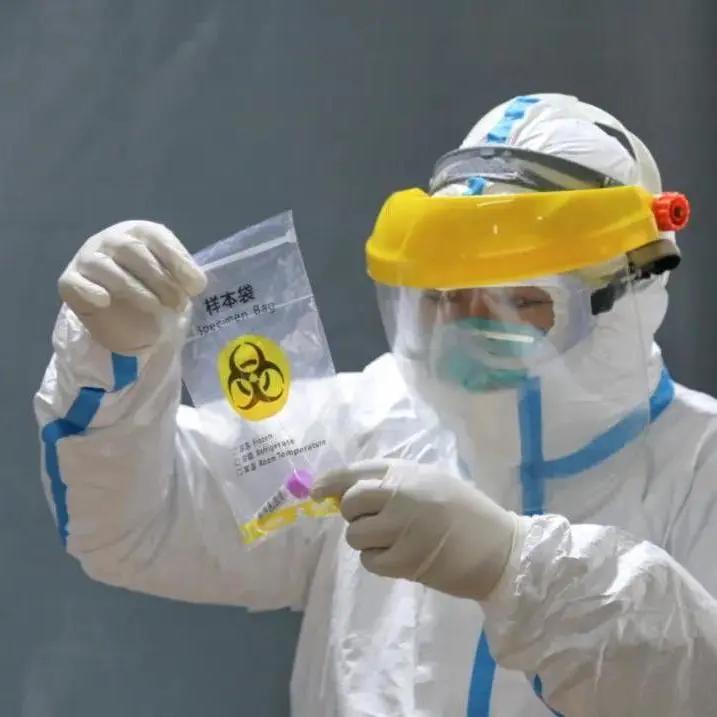
Sample preservation and disinfection
Non-inactivated samples are packaged in accordance with the WHO “Guidelines for the Transportation of Infectious Substances” in accordance with the UN2814 Class A infectious substances in PI602, and the inactivated samples are packaged in accordance with the UN3373 Class B infectious substances in PI650.
Before the sample transfer box is closed, the surface of the container must be disinfected by spraying with 75% alcohol or 2000mg/L chlorine-containing disinfectant.
Garbage and medical waste disposal
In the sampling site, a medical waste collection device should be set up to ensure timely removal and transportation, and 1000-2000 mg/L chlorine-containing disinfectant should be sprayed and disinfected regularly to prevent environmental pollution. Adequate personnel shall be provided for each sampling site to be responsible for the terminal disinfection of the sampling site and the transfer of medical waste.
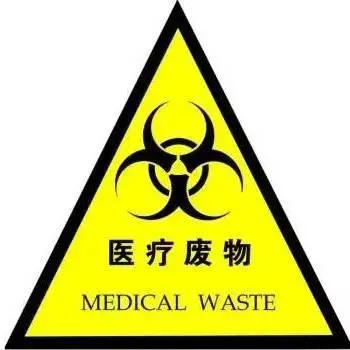
Disposal should follow the requirements of the “Medical Waste Management Regulations” and “Medical Waste Management Measures for Medical and Health Institutions”, standardize the use of double-layer yellow medical waste collection bags and then dispose of them according to the conventional disposal process.